-
The drum dryer uses hot air to dry the ribbon-shaped soap body. Bands on the right and left move to cause the ribbon shape soap body to go back and forth, subjecting it to an even stream of hot air that reduces its moisture content.
-
At the end of the drum dryer process, the moisture content of the soap body has been lowered to 12%. Next, the screw granulator turns it into noodle shapes of 10-15 mm in width and 5 mm in diameter (soap noodles). From there, it is processed into chips for easier mixing and kneading in subsequent processes.
-
The soap body is tested prior to transportation. A battery of tests measures things like the free alkali content, volatility and color. Only materials that pass the tests are used as toilet soap body. Air pressure transports soap body chips through a tube to fill flexible container packages for transportation to Fujikawaguchiko Factory.
-
The soap body chips from the Sumida Factory are put in a mixer for mixing. For some products, essential oils, plant extracts and other moisturizing components, and herbal powders may be added. Mixing is a careful, time-intensive process of unsticking chips that may have solidified during transportation and ensuring even application of the extracts and other ingredients.
-
The soap body moves from the mixer to the roller. During the transportation process, the outsides of the soap body chips dry and become hard while the insides remain soft. They are subject to double rolling in a vacuum to even out consistency.
-
The soap body moves from the roller to the extruder. As the body moves through the extruder, it goes through mesh to break it up into finer pieces. In the extruder, the soap body is heated and pressurized before being pushed through a specialized mouthpiece. This process is essential to producing smooth soap that is not easily cracked.
-
The soap body emerges as long, thin rods, each of which is stamped in its own mold. Stamping is where the soap is formed. This step not only makes the soap beautiful to look at, but also puts it in a form that is easy to hold and use.
-
After it is stamped, staff members pick up the soap in both hands and quickly arrange it on a drainboard. As they are doing this, they are also checking for any admixture of foreign substances, damage or discoloration, confirming that the soap is in the correct position for applying the carved seal, and making sure that it is not scratched.
-
Intermediate testing prior to packaging measures weight and other properties. Only soap that passes all tests is packaged. It is given a serial number, and the printing of the serial number is visually confirmed for each piece. Final testing after packaging ensures that only the highest quality soap is delivered to customers.
MANUFACTURING / Milling method
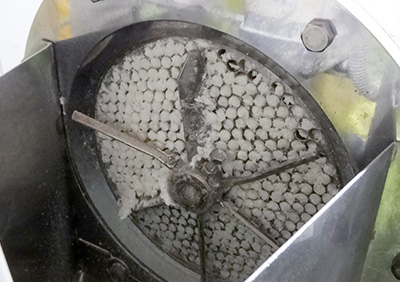
Hot gel-form soap body is dripped onto a cold roller drum, causing a thin layer to instantaneously solidify on the drum's surface. The solidified soap is then automatically raked into a ribbon shape before being sent to the dryer.